Compressed air treatment
During compression the compressed air becomes contaminated with water, dirt, wear particles and degraded lubricating oil. Their mixture constitutes unwanted condensate and becomes acidic. On delivery to the point of use, this abrasive sludge can destroy the very equipment it is meant to operate and, if not carefully re-moved can result in severe corrosion, can cause blockage in valves, increased maintenance and downtime, inevitably leading to reduced system efficiency.
The drying is the basic element for the compressed air treatment. It’s performed by using cold dryers or adsorption dryers. Another important elements in the process of compressed air treatment are after-coolers cooled by water or air, hypersep separators, tandem dryers, ANTARES, filters, condensate drains, oil/water separators.
REFRIGERATION DRYERS
Refrigeration dryers assure effective drying of compressed air to dew point 3⁰C and offer precise control of dew point and reliable operation in the range of 0-100% of dryer’s capacity.
The new series of compressed air refrigeration dryers StarlettePlus–E are assigned for flow rates in range of 24 – 372 m3/h. StarlettePlus-E has the lowest expenses for operations and the construction requires the smallest coolant volume (R134a) in it’s category.
The PoleStar Models (PST), respectively model PST 120 and larger has cleverly devised energy-saving feature SmartSave®. It means the dryer is controlled in the on/off mode, according to the system requirements. Thanks to SmartSave® it is possible to reduce the consumption of energy to a minimum during the night shifts, weekends or operational shutdowns. Water-cooled condensers are available on all PoleStar models from PST220 to PST1800.
Refrigeration dryers QSR have highly effective, water-cooled tube nest condenser with reduced pressure drops. The capacity of scroll type cooling compressors in “tandem” configuration is 225m3/min, with the low consumption of energy and minimal vibrations. They are practically indestructible.
- Controlled and managed by a sophisticated microprocessor (standard issue), with a display
- Illimitable possibilities of installation thanks to air inlet temperature of up to 65 ⁰C
- Air-cooled condensers are available as well
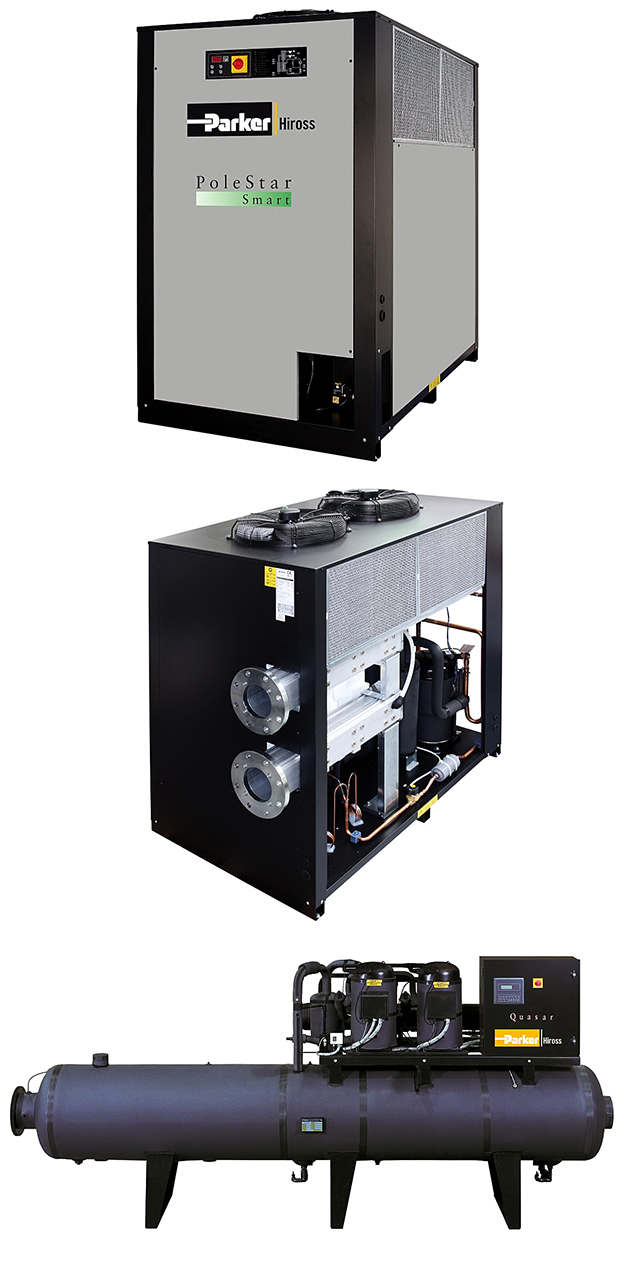
Refrigeration dryers
Type | Maximum air flow |
---|---|
SPL StarlettePlus-E (New) | up to 372 m3/h |
PST PoleStar Smart | up to 10 800 m3/h |
PSH PoleStar Smart (for high pressure) | up to 7 200 m3/h |
QSR Quasar | up to 21 000 m3/h |
LCD Large Capacity Dryer | up to 26 400 m3/h |
ABSORPTION DRYERS OF COMPRESSED AIR – PNEUDRI
Clean, dry air improves production efficiency and reduces maintenance costs and downtime. The PNEUDRI dryers deliver clean, oil-free and highest level of dry compressed air and at the same time offer the lowest cost of operation.
The PNEUDRI ranges of heatless and heat regenerative dryers have proven to be the ideal solution for many thousands of compressed air users worldwide in a wide variety of industries. PNEUDRI totally cleans and dries compressed air down to -40˚C pressure dewpoint (pdp) as standard. For critical applications, PNEUDRI can be specified to provide a pressure dewpoint of -70˚C pdp.
Saving energy with the dewpoint dependent switching (DDS) energy management system
The energy required to regenerate the off-line desiccant bed in an absorption dryer is constant, and based upon the assumption that the dryer is operating at its full capacity and the desiccant bed requiring regeneration has been fully saturated. In reality, a dryer is rarely operating at full capacity all of the time, for example during shift work and periods of low demand. With the DDS Energy Management system installed, the drying cycle remains unchanged, however as the drying chambers are about to change, the DDS system overrides normal operation to fully utilise the drying capacity of the on-line desiccant material. Using DDS will ensure that the energy consumed by PNEUDRI is directly proportional to the actual air flow, temperature and moisture loading, not the dryers rated capacity, thus providing significant energy (up to 75%) and environmental savings.
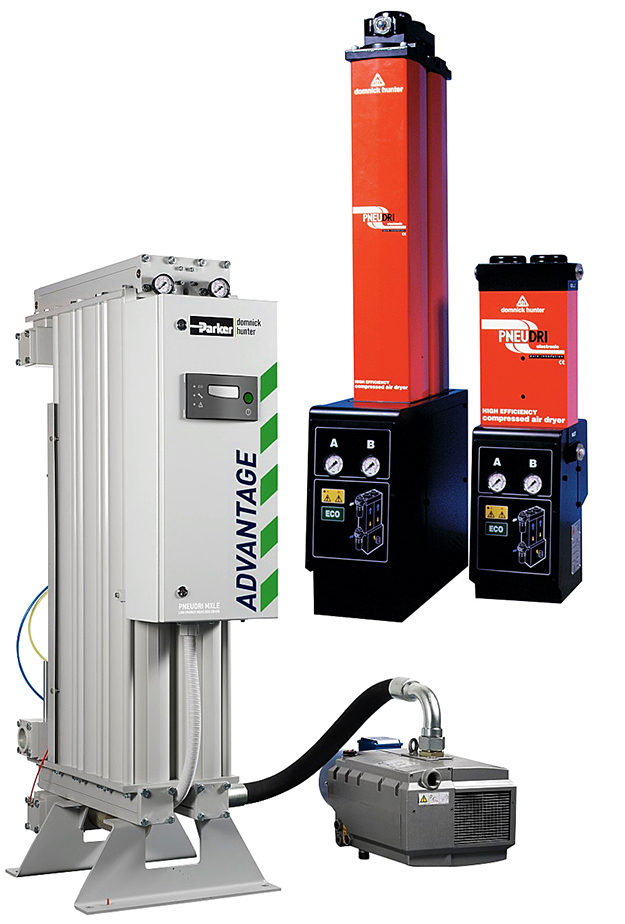
Adsorption dryers of compressed air – PNEUDRI
Type | Air flow | Reference conditions |
---|---|---|
PNEUDRI MiDAS (DAS) | up to 34 m3/hour | 7 bar g, sanie 20 °C + 1 bar abs |
PNEUDRI MIDIplus (DME) | 40 - 300 m3/hour | 7 bar g, sanie 20 °C + 1 bar abs |
PNEUDRI Maxi (MX) | 400 - 2 000 m3/hour | 7 bar g, sanie 20 °C + 1 bar abs |
PNEUDRI MXLE Advantage | up to 21 000 m3/hour |
CENTRIFUGAL WATER SEPARATORS, COMPRESSED AIR FILTERS, CONDENSATE DRAINS, OIL / WATER SEPARATORS
Hypersep Parker Hiross water separators utilise centrifugal technology for the effective removal of bulk liquid from a compressed air system; providing essential downstream protection as well as the added benefit of improving the performance of other downstream equipment.
Hypersep separators are very compact and easy to install and is offered with a full range of threaded and flanged air connections. It needs no external power source, and it works automatically without any maintenance requirements. Hypersep can withstand even the toughest industrial conditions.
Most problems experienced by compressed air users derive from contamination already in the compressed air system. These contaminats such as oil, rust, limescale need to be removed or reduced to acceptable levels.
Compressed air incorporates a high concentration of dirt, oil, moisture and other impurities. Hyperfilter has been specifically designed to prevent these undesired effects, offering a comprehensive range of compressed air filters covering all industrial needs.
The secret of Hyperfilter is its highly advanced borosilicate filter element. The borosilicate filter media offers an extremely high void volume, lenghtening the element’s life and cutting energy costs to a minimum.
The Hyperfilter range guarantees a complete filtration with the 5 filtration grades D (very low dew point filtration), Q (general purpose), P (fine filtration), S (oil-free filtration) and C (critical filtration). Hyperfilter filter media features a special treatment which ensures that the element actively repels both oil and water. Compared with typical filters this reduces pressure drops and, as a consequence, running costs, as well as ensuring a higher filtration efficiency.
Parker Hiross Hyperdrain / Ecodrain can be used with all components in the compressed air system. The condensate drain is a vital component in any compressed air system; its role is to guarantee an efficient removal of all the condensate and impurities present within the compressed air.
Even the smallest amount of liquid condensate, if carried through the compressed air network, can cause serious damage to apparatus and processes. It is of paramount importance that all condensate is completely removed from the compressed air circuit.
Parker ES2000 Series of static oil/water separators are designed to separate compressor oil from condensate without the use of external power.
Oil/water separators are installed as part of the purification system and simply reduce the oil concentration in the collected condensate. This leaves the relatively small amount of concentrated oil to be disposed of legitimately and economically. Oil/water separators help to protect and maintain the environment.
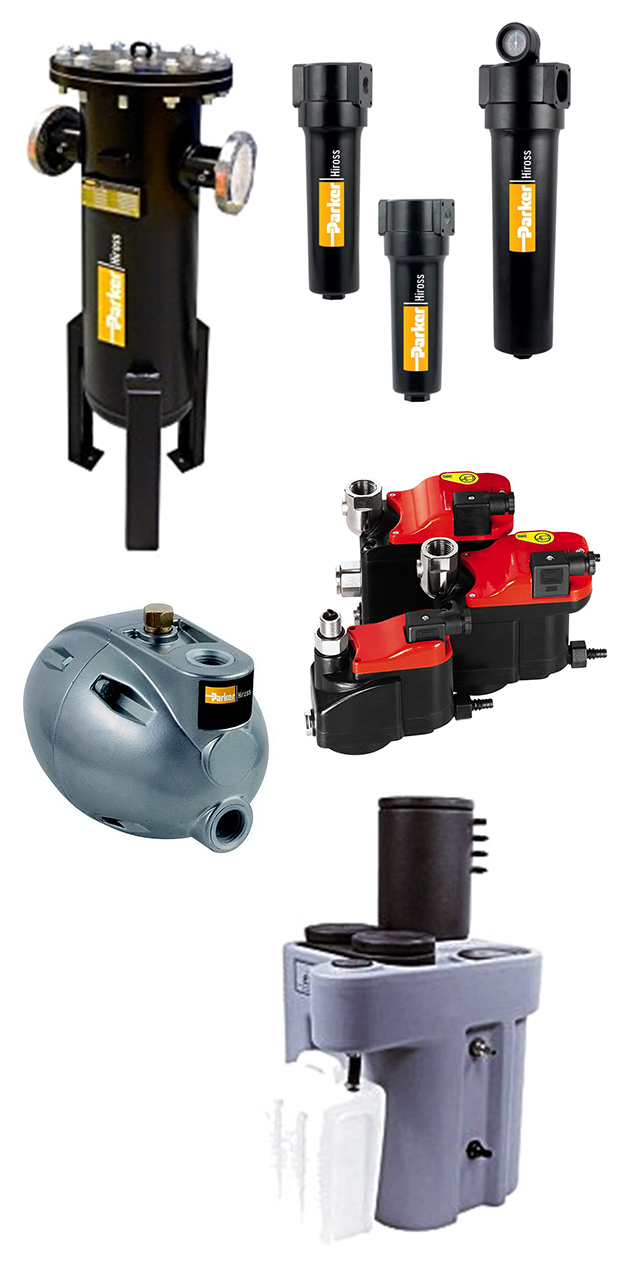