Nitrogen gas generators
NITROSource PSA generators
NITROSource PSA generators comprise of high tensile aluminium columns, each containing twin chambers of Carbon Molecular Sieve, (CMS), a material which removes oxygen and trace gases from compressed air by molecular adsorption, allowing nitrogen to pass through as the product gas.
PSA Nitrogen Generators utilize a combination of filtration and pressure swing adsorption (PSA) technologies. The gas separation process preferentially adsorbs oxygen over nitrogen using carbon molecular sieve (CMS). CMS is the material that removes the oxygen from the compressed air stream. This is the ‘engine’ of the generator, and the source of valuable performance benefits: more gas for less compressed air, reducing energy consumption; a very long working life – saving money on replacements; and less CMS per unit of gas produced, enabling a more compact unit. By raising and lowering the pressure within the CMS bed, all contaminants are captured and released, leaving the CMS unchanged.
Parker designs and manufactures generators, encompassing new concept – PSA (pressure swing adsorption) technology together with an advanced Energy Saving Technology (EST). A PSA nitrogen generation system separates nitrogen from oxygen based on the preferential adsorbtion and desorption of oxygen and other contaminants on carbon molecular sieve. Unique Energy Saving Technology (EST) dramatically reduces compressed air consumption and energy cost, by ensuring that the inlet compressed air flow is always exactly matched to the nitrogen gas outlet flow and purity.
Parker’s nitrogen generators operate at outlet nitrogen pressure up to 13 bar, meaning the another economical benefit in case there isn’t need for extra compressor to be added to nitrogen generator station.
NitroSource generators main parameters:
- Off-Gas By-Pass – automatically vents off out-of-specification gas
- Designed for over 10 year’s operational life without need of Carbon Molecular Sieve change
- NITROSource is the most economical source of nitrogen. It consumes less compressed air and energy than traditional generators – delivering substantial cost savings as well as greater sustainability in the long run. The NitroSource generators are appropriate for manufacturers and producers in a wide range of industries: food production, beverage and bottling, pharmaceuticals, materials processing, electronics, etc.
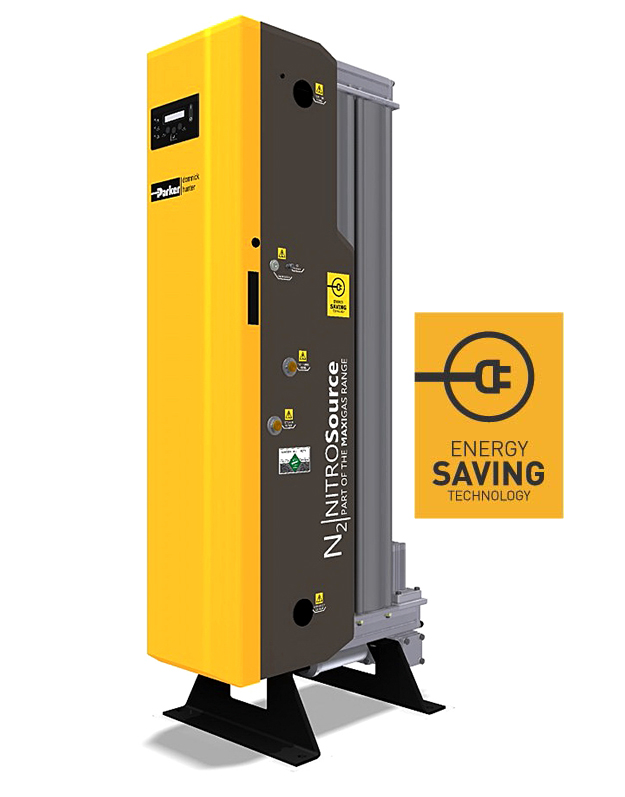
MEMBRANE NITROGENE GENERATORS
Parker’s nitrogen generators utilize proprietary membrane separation technology. The membrane separates compressed air into two streams: one is pure nitrogen and the other is air enriched with oxygen, carbon dioxide, water and other gases.
Dried compressed air (+3°C pdp) enters the gas generator inlet port where it passes through 1 micron and 0.1 micron filtration, then through a carbon tower to remove oil odour, vapour and ozone, a dust filter and then into the membrane modules. The membrane modules are designed to remove unwanted gases such as oxygen and water vapour through the hollow fibre wall and out to atmosphere, whilst retaining nitrogen as the product gas that is fed through to the application.
Compressed air is introduced into the center of the fibers at one end of the module and contacts the membrane as it flows through the fiber bores. Oxygen, water vapor and other trace gases easily permeate the membrane fiber and are discharged through a permeate port while the nitrogen is contained within the membrane and flows through the outlet port.
Process of separation
The concept of gas separation by hollow-fibre membranes is simple. A small hollow tube allows unwanted gases such as oxygen and water vapour to permeate through its walls whilst the product gas, nitrogen is retained for use as the product gas.
In reality, molecular separation is slightly more complex. Parker domnick hunter’s team of polymer scientists has refined and developed the advanced hollow-fibre technology to achieve extremely high levels of performance and stability. Parker domnick hunter hollow-fibre membranes are produced from a very strong engineering polymer – Polyphenylene Oxide, (PPO). As well as being robust, the PPO is also very permeable. This means that fewer fibres are needed for a given volume of nitrogen production and a much lower inlet air pressure is required for gas production to take place. In fact Parker domnick hunter membranes are the most permeable produced anywhere in the world.
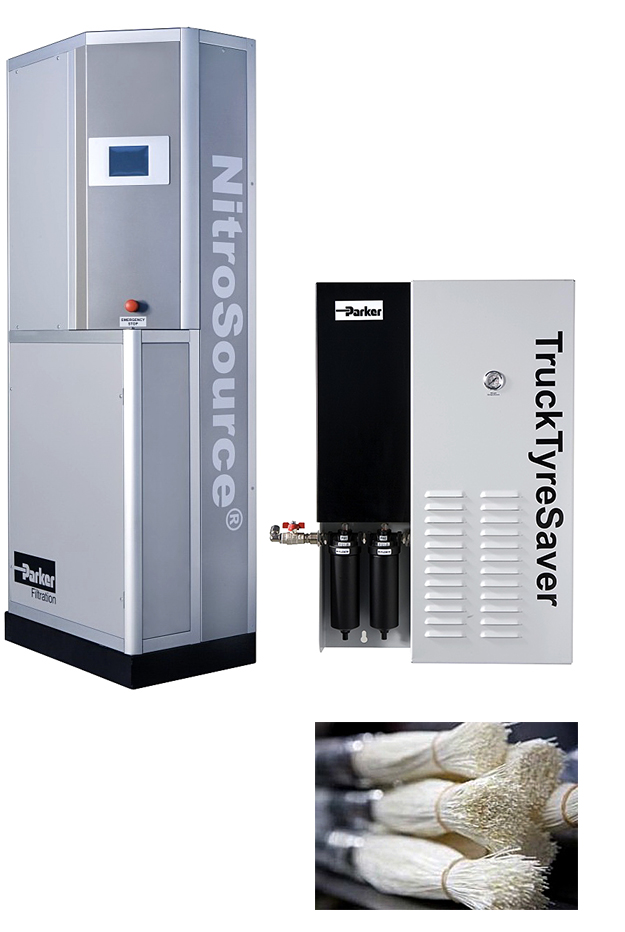